10 Leadership Barriers to Workplace Safety—And How to Fix Them
Closing the Leadership Gap for Stronger Safety Commitment
One of the most frequently cited challenges in organisational safety management is achieving genuine management buy-in. This issue is reinforced by regulatory codes of practice and international standards alike, making it a critical concern for both seasoned and new safety practitioners.
Discussing the necessity of leadership engagement in safety management brings to light an uncomfortable truth: safety is not always a top organisational priority, despite claims to the contrary. The phrase safety first, though widely used, has become somewhat distorted—implying it is the foremost priority, when in reality, management’s commitment often falls short.
In stark contrast, revenue generation and profitability remain unequivocal priorities for most organisations. Senior management is acutely aware of the supremacy of financial goals—if only because they ensure business continuity and, ultimately, job security for everyone, including themselves.
Moreover, poor safety performance tends to have a short media half-life—except in cases of catastrophic accidents. In today’s investor, regulatory, and consumer landscape, workplace safety performance often receives minimal scrutiny. As a result, organisations with weak safety records are not necessarily penalised when competing for new business opportunities.
For safety practitioners, securing genuine management buy-in—even for the most effective safety programmes— is an uphill battle. Yet, without it, making a meaningful impact remains nearly impossible. Against this backdrop, here are ten key barriers to leadership engagement and strategies to bridge them.
Barrier 1: Business and Cultural Norms that Prioritise Cost over Safety
The primary purpose of a for-profit organisation is to generate profit. Achieving this safely, sustainably, and ethically is a subset of that goal—not its entirety.
While the ideal scenario envisions safety and profitability as coexisting priorities, the reality often tells a different story. When critical decisions arise, an organisation’s true priorities become evident—profit frequently takes precedence, despite safety being publicly declared a top concern.
In many organisations, proclaiming safety as a priority has become a normative yet superficial stance. Leadership statements of safety first may be encouraging, but they often fail to translate into sustained action or meaningful cultural improvements. This disconnect leaves organisations ill-equipped to genuinely prioritise safety, creating a gap between stated values and operational realities.
For safety practitioners, the key strategy to overcoming this challenge starts with mastering the entire operation. This deep understanding allows them to identify the various subcultures and competing priorities that influence senior management’s commitment to safety. It also transforms the safety team into a valuable repository of operational knowledge—an asset to leadership.
When safety professionals are regarded as key contributors to overall operations, they gain leverage in promoting and embedding the safety approaches they advocate. Simply put, master the operation, and you’ll not only perform your role more effectively— you’ll also earn a seat at the decision-making table.
Barrier 2: Poor Understanding of the Value of Effective Safety Management
For the safety practitioner, securing a hard-won seat at the decision-making table is only the beginning of implementing a successful safety management system. Selling the value of effective safety management is a formidable challenge, partly due to factors external to the organisation that nonetheless have a significant impact on it.
Investors evaluating companies meticulously analyse various metrics, including market capitalisation, total revenue, and total addressable market, along with dozens of other financial indicators. This detailed scrutiny, enabled by publicly available data, allows for direct comparisons between companies operating in the same industry.
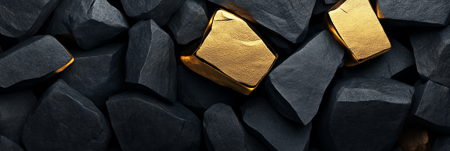
However, conducting a similar comparative analysis on safety performance across corporations is nearly impossible. Publicly available safety metrics are scarce, and when they do exist, they are often inconsistent and lack standardisation. This makes it difficult—if not impossible—to draw meaningful comparisons between competitors’ safety performance.
The disparity between accessible financial data and the limited visibility of safety performance leads to a skewed perception of safety management’s actual value. Without clear, comparable metrics to highlight safety performance, senior management may continue to sideline safety priorities, even while outwardly affirming their importance.
Addressing these external limitations is beyond the control of any individual safety practitioner. Instead, practitioners must leverage their deep understanding of operations to align regulatory compliance with operational efficiency. For example, streamlining the offloading of materials in a way that is both safer and faster creates tangible efficiency gains.
Demonstrating the value of safety to senior management will not come from external sources such as published research or marketing communications. Instead, it will stem from safety-driven operational refinements that yield measurable efficiencies. The role of the safety practitioner is to use their in-depth operational knowledge to identify and implement these opportunities, document and promote them.
Barrier 3: Conflation of Safety and Accident Prevention
Even when the value of effective safety management is recognised, its implementation is often fraught with challenges. Senior managers tend to focus on issues directly tied to their operational duties, leading to the recurring question: Isn’t safety just about accident prevention?
While accident prevention is already a significant task for any operations team, seeing beyond it remains a challenge for many management teams. Yet, a safety management system designed solely for accident prevention is unlikely to succeed.
Merging the concepts of safety and accident prevention oversimplifies a complex issue. It’s akin to suggesting that peace is merely the absence of war. Accidents result from a complex interplay of factors, leading to outcomes ranging from negligible to catastrophic.
Proactively addressing seemingly minor issues that contribute to accidents is crucial, because once the immediate conditions for an accident are set in motion, control over the outcome is largely lost. Many of these immediate conditions stem from systemic issues that will continue to create similar risks until they are properly addressed.
For example, in operational environments where workers’ opinions are seldom sought, a culture of underreporting develops. While underreporting in some areas may not pose significant risks, failing to report safety-critical issues can be catastrophic.
Expecting workers in such environments to make exceptions and report only safety issues is a false hope. Instead, these settings tend to suppress feedback from the field, heightening the risk of accidents. Improving general communication between field teams and management is not just a safety initiative—it is an overarching organisational improvement with significant safety implications.
After all, the Safety culture of an organisation never exists in isolation of all the other cultures and subcultures within it.
A strong strategy for safety practitioners seeking to demonstrate that safety transcends accident prevention is to extend their influence beyond it—into areas of operational efficiency that have safety implications. Poor standards in other aspects of operations are often magnified in safety, not reduced.
Barrier 4: Confusion Surrounding Responsibility for Safety
With the case for safety management extending beyond accident prevention firmly established, a common issue across many organisations is the uncertainty surrounding responsibility for safety. This is exacerbated by confusion surrounding the use of terms like responsibility, authority and accountability.
While these terms are not explicitly defined in ISO 45001, their use in the standard suggests the following distinctions: responsibility relates to whose job it is, authority refers to who has the power to act, and accountability indicates who will be answerable for it.
Under ISO 45001, the ultimate responsibility and accountability for ensuring workplace safety rest with top management. While the standard allows for delegation of authority and assignment of responsibilities, top management retains the final accountability for the safety of the organisation.

Ensuring clarity in these delegations, responsibilities, and authorities is essential. Without it, confusion seeps in. Safety managers may argue that safety is a line management responsibility, while line managers, in turn, question the necessity of the safety team.
This dilemma is not exclusive to organisations with nascent safety cultures; it is equally prevalent in those that claim to have mature safety cultures. It often stems from an inability to distinguish between senior management’s ultimate responsibility for overall safety and the immediate responsibilities for specific aspects that contribute to it.
An effective approach is to ensure that senior leaders understand their own responsibility and accountability for safety, as well as their ability to assign responsibilities and delegate authority appropriately within the safety management system. The role of the practitioner is to ensure that such delegations and assignments are valid—meaning those assigned responsibilities also have the authority to act—and that these are communicated clearly.
Barrier 5: Poor Integration of Safety Roles and Responsibilities
Regardless of the roles assigned to safety team members and operations line managers by senior leadership, gaining true leadership buy-in and engagement depends on how well safety roles and responsibilities are integrated into overall operations.
For safety management to take root within an organisation, safety roles and responsibilities must be seamlessly embedded into daily operational tasks rather than treated as standalone functions.
When safety-related elements—such as risk assessment briefings—are treated as an afterthought or merely an addendum to primary tasks, their implementation becomes inconsistent, often sidelined in favour of more immediate operational pressures.
Embedding these elements directly into operational processes makes them feel natural and habitual— a positive outcome for long-term safety performance.
One effective strategy is to distribute risk assessment briefings across different stages of the operation rather than condensing them into a single session before work begins. The ability to implement this seamless integration while still meeting regulatory requirements is a fundamental skill for a seasoned safety practitioner.
Barrier 6: Poor Integration of Safety into Management Progression Metrics
One key barrier that can be addressed at the senior management level—without requiring major system-wide changes— is the way safety is linked to the career progression of senior managers.
Safety achievements rarely top the list of qualifications that propel individuals into senior management positions. Typically, promotions are based on metrics other than safety performance. Simply adding safety as a criterion in performance appraisals, as has become common, often yields limited impact.
Instead, safety responsibilities should be woven into the fabric of all organisational roles, supported by transparent metrics that make safety performance a natural part of performance evaluations.
For instance, assigning a senior manager the responsibility of overseeing ongoing coordination of residual risk information between designers and site operations teams reinforces safety as a fundamental aspect of their role.
Providing managers with support in these responsibilities, documenting their performance, and highlighting their safety contributions in performance reviews can transform safety from a mere formality into a meaningful component of professional achievement.
This approach goes beyond superficial participation in safety walks, fostering a culture where safety is embedded as a default, integral part of management duties.
Barrier 7: Perceived Onerousness of Safety Initiatives
Even when senior managers are genuinely committed to prioritising safety, they often face the challenge of safety initiatives being perceived as overly burdensome. Many safety measures are seen as add-ons to regular operations—rarely essential to completing the tasks at hand.
Unlike a traffic light, which may interfere with the smooth flow of traffic but whose absence would undoubtedly make conditions worse, few safety initiatives fall into this category of being inconvenient yet essential. Instead, most are perceived as inconvenient and essential only for legal compliance, rather than for their intrinsic value in improving safety.
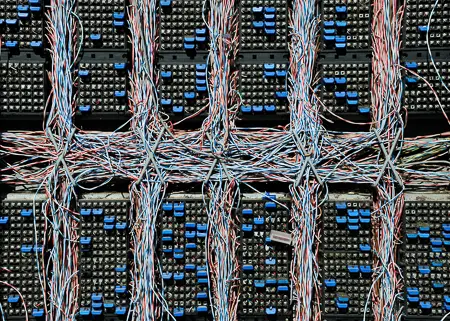
Of course, the benefits of many safety requirements go far beyond avoiding prosecution. However, it is easy to see why this perception of superfluity persists.
Until these critical safety elements are inextricably embedded within the operation itself, they will continue to be seen as unnecessary add-ons—onerous tasks that are quickly discarded when production pressures rise.
A strategy to eliminate the perceived burden of safety initiatives is to integrate them seamlessly into the operation itself.
For example, coaching a team leader to disseminate risk assessment requirements in real time, as the job progresses, ensures that safety briefings are part of the natural workflow rather than an awkward pre-task formality.
Take a raft pour, for instance. Various team leaders who have studied the risk assessments—ideally having been involved in their creation— can relay safety requirements as part of their ongoing duties. The carpenters get briefed as they compete their final checks before the pour, the survey team as they confirm levels, the pump operator is briefed upon arrival, and workers get theirs ahead of the pour. These briefings feel natural and become habitual.
The team leader then records confirmation of these briefings in their daily report— another task that fits seamlessly into operational workflows. In this way, safety becomes an integral part of the job, not an addendum to it.
Barrier 8: Traditional Management vs. Workers Standoff
The safety culture of an organisation does not exist in isolation from other workplace cultures and subcultures. It is either enhanced or eroded over time by broader organisational dynamics. One such influence is the often adversarial relationship between management and workers, as seen in union-management disputes.
Although this relationship has evolved over the years, elements of its adversarial past have never fully disappeared. Safety, rather than being an area of agreement, has historically been a point of contention—and in many cases, rightly so.
A practitioner who understands this relationship, its adversarial history, major trends, and its current standing is better equipped to navigate the challenges it presents in securing senior management buy-in for safety initiatives.
A strong strategy is to create win-win narratives that resonate with both management and workers. This approach is supported by most regulations, which recognise the critical role of workers in managing safety. Standards such as ISO 45001 further reinforce this by incorporating multiple requirements for worker consultations as essential elements of compliance.
Barrier 9: Inadequate Research on the Efficacy of Safety Initiatives
With a firm grasp of the financial constraints of their operations, senior managers have a natural tendency to demand that proposed safety solutions and initiatives provide the best value for the resources invested. However, research into the effectiveness of safety initiatives remains limited beyond marketing claims.
This barrier extends beyond the capability of any single practitioner—it is an industry-wide challenge. The question of what constitutes good safety performance is long overdue for a rigorous, empirical answer.
Until comprehensive research fills this gap, practitioners can implement internal data collection for benchmarking safety performance over time. Leveraging these findings can help persuade senior managers to support safety initiatives based on measurable improvements.
Barrier 10: Resistance to Change
Resistance to change is a pervasive issue within organisations, particularly when initiatives are perceived as adding little value to an individual’s role. This resistance intensifies when tasks are seen as ancillary or, worse, obstructive to primary duties.
The appeal of quicker, more straightforward methods often overshadows the commitment to safety. The safest approach isn’t always the fastest or most cost-effective, typically requiring additional time and resources, which can provoke frustration and pushback.
Furthermore, the persistence of organisations operating with suboptimal safety records—without immediate consequences— reinforces a reluctance to change. In industries where a company’s next project or opportunity seldom hinges on tangible, comparative safety metrics, the incentive to overhaul existing practices diminishes.
This raises a critical question: in the absence of direct consequences or competitive disadvantage, what motivates an organisation to adopt higher safety standards?
One way to overcome this barrier is to recognise that without closely aligned, deeply held principles, change is difficult and takes time to embed. By understanding industry dynamics and the organisation's broader culture, even small-scale changes can be leveraged as significant wins, paving the way for larger successes. This empathetic approach may be the key to securing senior leadership’s commitment to more substantial transformations.
In conclusion, securing leadership buy-in for safety is a formidable challenge, with numerous obstacles seemingly stacked against it. Successfully navigating this landscape requires a combination of skill and diplomacy, particularly in environments where genuine commitment is lacking and the temptation to feign engagement is high.
However, the ten barriers outlined here should not be a cause for discouragement. Instead, they highlight key areas for growth and improvement, offering opportunities to refine strategies and drive meaningful change in safety culture.
At SafetyRatios, we challenge leadership norms in safety management by bringing real-world operational insights into thought leadership. This article is part of our leadership-focused approach—explore strategies to overcome barriers to safety engagement on our Solutions Page and discover management-focused safety tools with a free trial.