ISO 45001 Organisational Context: 5 Common Mistakes to Avoid
Key Pitfalls in Context Analysis and How to Overcome Them
The first step in achieving ISO 45001 compliance is conducting a thorough organisational context analysis (Subsection 4.1). A well-defined ISO 45001 management system requires a deep understanding of internal and external factors that influence occupational health and safety performance.
Just like a design brief for engineers, a client appraisal for consultants, or a patient history for medical professionals, an organisational context assessment lays the foundation for an effective safety management system (SMS). Without this, the system risks misalignment with business objectives and workplace safety regulations.
A risk-based approach to safety management requires organisations to identify operational strengths, weaknesses, and potential hazards before implementing controls. Failure to do so leads to compliance gaps, inefficiencies, and increased risk exposure.
However, many organisations rely on generic, pre-made ISO 45001 templates that lack relevance to their specific safety culture and operational environment.
Copy-pasting from one company to another may satisfy audit requirements but fails to enhance hazard identification, incident prevention, and overall occupational health and safety (OHS) performance. This oversight can impact long-term regulatory compliance, operational efficiency, and employee well-being.
Below are five critical mistakes that organisations make when conducting an ISO 45001 organisational context analysis— and how to avoid them.
Why Organisational Context is the Foundation of ISO 45001 Compliance
One of the most common yet often overlooked mistakes is a poor understanding of the centrality of organisational context. Subsection 4.1 is the heart of ISO 45001. It is where the bulk of the development time for designing a management system should be spent— much like sharpening the axe before cutting, in reference to Washington’s famous saying.
Subsection 4.1 is not just one of many subsections within the standard; in reality, it deserves to be a standalone section to emphasise its importance.
It states that: The organisation shall determine external and internal issues that are relevant to its purpose and that affect its ability to achieve the intended outcome(s) of its OH&S management system. In other words, the organisation must understand where its management system is likely to succeed or fail.
In practice, compliance with Subsection 4.1 is a consultative process where individuals with deep knowledge of the company’s past, present, and future operations provide insights into the key issues affecting the organisation. This is not a task for an external consultant alone—it requires the input of frontline staff, sales teams, long-standing employees like Stacey, who has been with the company for 40 years, and Ali, who worked for the owner's grandfather.
Determining internal and external issues is a task best handled by insiders, seasoned employees, and frontline staff. The role of a consultant in this process is to facilitate the analysis, guiding it with structured methods such as SWOT, PESTLE, and other analytical tools.
The choice of tools should be informed by a thorough understanding of the organisation’s nature, making this an iterative process. The consultant, working alongside insiders, experienced employees, and forward-thinking staff, should first develop an initial understanding of the organisation. Based on this, they can select an appropriate analysis tool, conduct an initial assessment, and refine the approach as necessary—potentially introducing additional tools to enhance the analysis.
Who Should Be Involved in ISO 45001 Context Analysis?
A second, closely related mistake in analysing an organisation's context is selecting the wrong people for the analysis. If leadership is too busy or too senior to engage in brainstorming sessions, the result will be a generic analysis that could apply to almost any organisation—rarely fitting the one in question.
Even among organisations in the same market, the success or failure of their management systems is tied to their unique characteristics, not just industry trends. Leadership must, therefore, play a central role in this analysis, not least because they set the organisation’s direction.
The absence of leadership in the brainstorming process is often an early indicator of poor commitment to safety, revealing how central—or peripheral—safety is within the organisation. Meanwhile, omitting frontline staff from the analysis results in a safety management system that exists only on paper and is never truly applied.
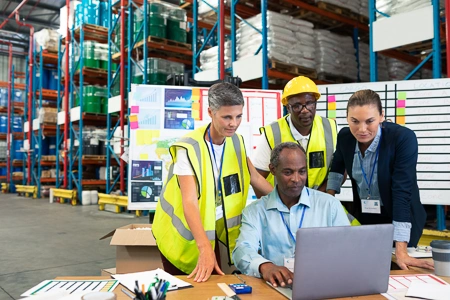
Top leadership, frontline staff, and all levels of management must be involved in identifying external and internal issues that are relevant to the organisation’s purpose and that affect its ability to achieve the intended outcome(s) of its OH&S management system.
Leaders contribute their knowledge of growth strategies and financial constraints. Frontline staff understand what works in practice and what does not. Middle managers have insights into the daily challenges that frontline staff face and how senior leaders respond to them.
Sales teams know what sells and what competitors are doing. Strategists understand emerging industry trends. The safety team is well-versed in legal requirements, while HR knows the organisation’s capacity and capabilities.
The skill of the consultant or management system designer lies in approaching these centres of organisational knowledge with tact, extracting the insights crucial to a meaningful analysis. There is no requirement to gather everyone in a room for half a day with sticky notes and markers. The goal is an analysis that has benefited from the full breadth of the organisation's knowledge.
Involving the right people in the analysis also has the added benefit of familiarising different levels of the organisation with the key components of the management system. This fosters a sense of ownership that no other form of communication can achieve.
A culture of trust and care, like safety culture itself, is not willed into existence simply because a team desires it. It requires dedication, skill, and time to become embedded, and its benefits remain inaccessible until then.
Choosing the Right Tools for Organisational Context Analysis
There are dozens of tools available for analysing the internal and external issues affecting an organisation. Some may have already been applied to the organisation in its financial and business strategy planning.
While certain tools may be useful in identifying OH&S-relevant factors, others may not. The skill of the consultant or systems designer lies in selecting the right combination of tools that complement the data already generated about the organisation.
The literature on SWOT, PESTLE, IPO, and other analysis methods is extensive, as is their application to safety management systems. A skilled safety management system designer is like a master painter who understands their tools and seamlessly switches between them in real time.
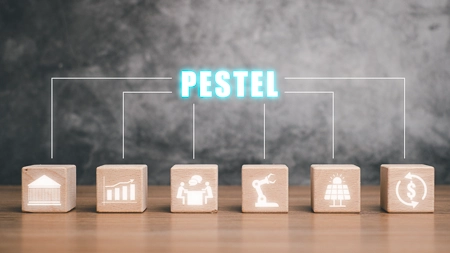
ISO 45001 does not mandate the use of specific tools; it simply requires that the process be systematic to ensure that all internal and external factors are given adequate consideration.
The choice of tools for analysing the organisational context depends on multiple factors, including the skill and experience of the systems designer, the availability of time, and the expertise of the participants contributing to the analysis.
Ultimately, the right tool is the one that best facilitates the identification and analysis of key issues. Internal participants should validate the identified issues, while the consultant ensures the integrity of the analysis.
ISO 45001 Documentation Requirements: What You Must Know
Despite significant advances in computing, paper-based documentation remains prevalent in almost all management systems. This often fuels the misconception that a management system must be written down.
The key focus should be on the word "system"—a system is not inherently paper-based or even document-based. Where documentation is necessary, it should be created, but producing dozens of pages that reduce accessibility only hinders the effectiveness of the safety management system.
Furthermore, Subsection 4.1 does not explicitly require that the information generated from the analysis be documented. The analysis of the organisational context is a foundational process that informs other stages in the development of the management system. Its primary output is not extensive flow diagrams or reports but actionable inputs into other elements of the system.
The ISO 45001 guidance document, ISO 45002:2023, clarifies this by stating: "An organisation can choose to document this information if it wants to adopt a more structured approach to its OH&S management system. However, the absence of such documentation should not impact the organisation’s ability to demonstrate conformity to ISO 45001, provided it can evidence a structured approach by other means."
Misunderstanding the documentation requirement for organisational context analysis can turn the process into an end rather than the means it is intended to be. Gaining an understanding of the organisation is the first step (a process) toward designing a safety management system, and it should be treated as such.
A well-executed analysis yields actionable insights and is preserved in a format that allows for future review and refinement. If documenting it in writing is the preferred approach, that is acceptable—but it is by no means the only way to achieve an effective analysis.
How to Integrate Context Analysis into Your Safety Management System
One direct consequence of (inadvertently) treating the organisational context analysis as an end rather than a means is that its findings often fail to be properly integrated into the management system it is intended to guide.
Poor integration of the analysis results also commonly stems from a misguided intent behind implementing a management system in the first place. If the primary goal is ISO 45001 compliance merely to meet client requirements or market status, then achieving certification becomes the focus—rather than establishing a strong foundation, which is far more critical to the organisation’s long-term success.
ISO 45001 compliance should be the natural outcome of a well-functioning safety management system, rather than the sole objective.
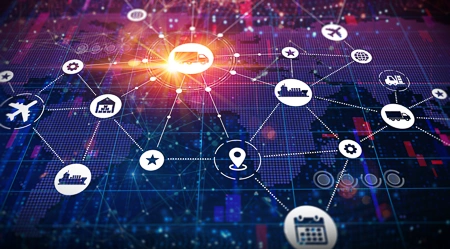
A truly robust management system should inherently align with ISO 45001. If it does not, that would be more of an indictment of the standard than of the system itself. ISO 45001 is a management standard, not a rigid specification like fixed values for paper sizes or thickness, which includes precise values. Section 1 of the standard explicitly states: "This document does not state specific criteria for OH&S performance, nor is it prescriptive about the design of an OH&S management system."
A sound approach to designing a safety management system is to base it on a thorough understanding of the organisation's context, tailor it to the organisation’s strengths and operational environment, and then conduct a gap analysis to ensure alignment with ISO 45001 requirements.
Designing a system with ISO 45001 compliance as the primary objective is also a valid approach, but it carries a higher risk of resulting in a "box-ticking" system that is detached from the organisation’s realities.
A management system is a living framework that both influences and is influenced by other subsystems within an organisation—it is not a standardised, off-the-shelf product. While purchasing a pre-designed system may work to some extent, it will likely fall short in fully addressing the unique needs of the organisation.
Ultimately, the focus of designing a safety management system should be on its objectives—objectives that can only be validated and achieved if the organisation's context is thoroughly understood.
A management system designer and key stakeholders must recognise the centrality of understanding the organisation’s context in relation to its legal obligations, growth strategies, and overall goals.
The analysis of organisational context should incorporate inputs from all centres of knowledge within the organisation— from the frontline to the boardroom. When seniority leads to self-exclusion or junior staff are perceived as irrelevant, the resulting analysis becomes a weak and ineffective data point for designing a robust management system.
To maximise the time commitment of participants in context analysis sessions, the consultant or systems designer must carefully select appropriate tools for each stage of the analysis. The key deliverable from this entire process is not a report but valuable insights that feed into later stages of system design.
Frequently Asked Questions
Organisational context in ISO 45001 refers to the internal and external factors that influence an organisation’s ability to achieve its occupational health and safety (OH&S) objectives. These factors include:
- Internal factors such as leadership commitment, corporate culture, workforce capabilities, and available resources.
- External factors like regulatory compliance, industry risks, stakeholder expectations, and economic conditions.
A well-defined organisational context ensures that safety management systems are aligned with real-world operational challenges and compliance requirements.
Organisational context analysis is a key requirement in ISO 45001, as it determines how effectively an OH&S management system integrates with business operations. A structured approach helps organisations:
- Identify workplace hazards and assess operational risks.
- Ensure compliance with safety regulations and industry standards.
- Align safety objectives with organisational goals and stakeholder needs.
- Improve decision-making and resource allocation for risk mitigation.
Without a structured organisational context analysis, safety management systems may fail to address key risks, leading to non-compliance and operational inefficiencies.
Several strategic analysis tools help organisations assess their internal and external context for ISO 45001 compliance, including
- SWOT analysis which evaluates strengths, weaknesses, opportunities, and threats related to safety management.
- PESTLE analysis which examines political, economic, social, technological, legal, and environmental factors impacting safety performance.
- Stakeholder mapping which identifies key stakeholders and assesses their influence on OH&S policies.
- Risk-based thinking, which integrates proactive hazard identification and risk assessment into decision-making.
Choosing the right tools ensures a data-driven approach to organisational context analysis, enhancing the effectiveness of the safety management system.
Many organisations make common mistakes when conducting organisational context analysis for ISO 45001, including:
- Relying on generic templates instead of conducting a customised analysis.
- Failing to engage key stakeholders, such as frontline employees, senior management, and regulators.
- Overlooking emerging risks, including new safety regulations and industry trends.
- Focusing only on compliance rather than implementing continuous safety improvements.
- Not integrating findings into the overall OH&S management system.
Avoiding these pitfalls ensures that organisational context analysis strengthens safety performance and regulatory compliance.
A structured approach to organisational context analysis helps businesses enhance workplace safety by:
- Identifying specific workplace hazards and improving hazard control measures.
- Ensuring safety objectives are aligned with actual operational risks.
- Encouraging proactive safety measures rather than reactive responses.
- Strengthening accountability and fostering a culture of continuous safety improvement.
Effective organisational context analysis supports risk mitigation, regulatory compliance, and the long-term success of the safety management system.
This article explores the common mistakes in assessing organisational context, their impact on safety performance, and how to avoid them for a more effective occupational health and safety (OHS) management system. For solutions that enhance risk assessment, safety culture development, and compliance tracking, visit our Solutions Page and explore our tools designed for safety excellence.