ISO 45001:2018 – Clause 4.1 in Action
The Basis of the Safety System — Applied Where Work Happens
Clause 4.1 isn’t just the starting point of ISO 45001 — it’s the part that makes the rest of the system real. It asks a simple but powerful question: what’s going on around you, and how does it affect safety?
From shifting teams and tools to deadlines and weather, context shapes the risks people face and the controls that work. When safety systems ignore what’s changing, they become outdated — or worse, irrelevant.
This field brief explores how Clause 4.1 applies in day-to-day operations. It highlights what to notice, what to ask, and how to make sure your OH&S system stays grounded in the realities of your work.
What Clause 4.1 Really Means
Clause 4.1 is about recognising that safety doesn’t happen in a vacuum. It’s shaped by what’s going on — in your team, on your site, and around your business. That includes who’s involved, what pressures you’re under, what’s changing, and how people actually get the job done.
When that context is understood and shared, the safety system can adapt. Procedures become relevant, controls feel real, and people are more likely to follow them. It’s not about listing everything — it’s about noticing what matters and making sure the system responds.
Understanding contextisn’t a paperwork exercise. It’s a mindset — one that starts with awareness and turns real-world insight into stronger, more useful safety decisions.
Practical Tips and Review Questions:
-
Can those responsible for safety articulate what “organisational context” means in your setting? If not, there's a risk Clause 4.1 is being treated as a formality rather than a foundation.
-
Is there a routine way for people to highlight what’s changed — in work, teams, tools, or expectations — so those changes can shape the safety system?
-
Does insight into the organisation’s context lead to changes in planning, risk controls, or leadership priorities — or is it treated separately from decision-making?
-
Is the idea of “context” explained in ways that workers and team leads can relate to? If not, the concept risks staying abstract or unused.
-
Does your OH&S system reflect what people actually experience on site — or does it feel disconnected from day-to-day realities?
Why It Matters on the Ground
When context is taken seriously, safety becomes something that fits the work — not something imposed from above. The system starts to reflect how tasks are really done, not just how they were imagined in a distant office.
Using context well helps spot new risks early, close the gap between rules and reality, and reduce the number of workarounds. It builds trust because people see that the system responds to what they’re actually dealing with.
Whether it's planning a job, setting controls, or reviewing performance, context keeps the safety system grounded — and that makes it stronger, faster to adjust, and more likely to be used.
Practical Tips and Review Questions:
-
Are the procedures people are expected to follow aligned with how the work is really done — or are there regular workarounds and informal fixes in play?
-
Is your current system sensitive to emerging risks — such as from new tools, shifting deadlines, or changes in crew — or do changes tend to go unnoticed until problems arise?
-
Are there parts of your OH&S system that feel outdated, irrelevant, or overly generic to those on the ground? If so, what practical updates could close the gap?
-
Do workers feel the safety system helps them do the job better and safer — or do they see it as something to work around or ignore?
-
When tasks are being planned, is context — like workforce mix, site layout, recent incidents, or external pressures — actively considered in how risks are managed?
What to Watch For: Common Context Triggers
Context isn’t static — it shifts all the time. Spotting those shifts early helps keep the safety system relevant. Some changes are obvious, like a new tool or a different crew. Others are more subtle, like rising time pressure or small changes in how tasks are done.
Key triggers to watch for include new team members, unfamiliar materials or equipment, changes in client expectations, or even weather conditions that alter how work is approached. These aren’t just operational changes — they often bring new risks or weaken existing controls.
The earlier these changes are noticed and shared, the quicker the system can adapt. Context awareness isn’t about big reviews — it’s about paying attention to what’s different today, and using that to guide what happens next.
Practical Tips and Review Questions:
-
Does your SMS include clear examples of context triggers — like new staff, changes in tools, or time pressures — so that they’re recognised early and consistently across sites?
-
Do workers feel confident identifying when something — or someone — on site has changed in a way that could affect how work is done or how safe it is?
-
Are minor but meaningful changes — like new task sequences, different environmental conditions, or updated client instructions — being captured before they compound into bigger risks?
-
Does a shift in context reliably trigger a review or update of the relevant risk assessments or procedures — or are changes noticed but not acted on?
-
Is your team encouraged to see change as part of the work environment — and therefore part of safety management — or is it only addressed when something goes wrong?
Fit Check: Does the System Match the Work?
A good safety system should feel like it belongs on your site. That means the controls make sense, the procedures reflect how tasks are actually carried out, and the language used is clear to the people doing the work.
If the paperwork says one thing but the job is done another way, something’s out of sync. When that happens, people start ignoring rules, and the system starts losing credibility. Fit checks help make sure that what’s written down matches what’s really happening — not just what was planned.
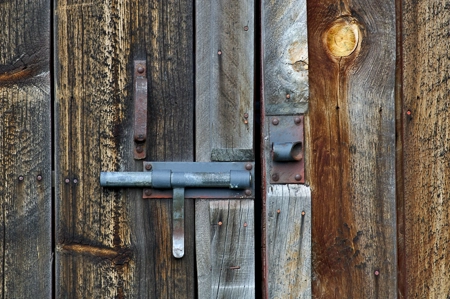
A system that fits builds confidence. It shows people their work is understood, and that the rules aren’t just for show — they’re there to help get the job done safely.
Spotting the Gaps
Even strong systems can drift out of step if no one’s watching for change. One sign is when tasks are being done in ways that aren’t reflected in the procedures. Another is when tools, roles, or risks have changed — but the controls haven’t.
If workarounds are the norm or people have stopped raising issues because nothing changes, the system isn’t keeping up. These gaps don’t just affect compliance — they affect trust, safety, and performance.
Spotting the gaps is about listening, observing, and asking: does this still make sense for the way we work now? If not, the gap isn’t the worker — it’s the system.
Speaking Up About What’s Changed
Keeping the system useful means speaking up when things shift. That doesn’t need to be formal — toolbox talks, handovers, and shift briefings are all moments to call out changes that affect how safe work is.
If something feels different — a new person, tighter deadlines, unfamiliar materials — flag it early. The sooner it’s shared, the easier it is to respond before it turns into a risk.
It’s not about waiting for permission. Everyone on site plays a role in keeping the system aligned. Sharing context isn’t extra — it’s essential.
How the System Should Respond
A responsive system doesn’t just collect feedback — it acts on it. When someone raises a change in context, that should trigger updates: refreshed risk assessments, adjusted controls, or even just clearer explanations from leadership.
People notice when nothing changes — and they stop reporting. But when feedback leads to visible follow-up, it builds trust. Over time, those adjustments don’t just fix issues — they become part of how the system learns and improves.
If the safety system is alive, it should move with the work. And that means showing that what people raise actually shapes what happens next.
Staying Audit Ready
Being audit ready doesn’t mean perfect paperwork — it means being able to show how the system reflects what’s really happening now. If you can explain what’s changed, how procedures have adapted, and where your input went, you’re already ahead.
Auditors want to see that safety controls are current, relevant, and informed by the people closest to the work. If you’ve had a say in reviews or updates, that’s evidence of an active system — one that values real input, not just documentation.
A strong system makes sense to the people using it. When that’s true, audit conversations become easier, because what’s on paper matches what’s on site.
Practical Tips and Review Questions:
-
Are site leads and safety reps able to clearly explain recent shifts in the organisation’s context — and how those shifts have influenced planning or control measures?
-
Do your documented procedures and risk controls reflect current operating conditions — or are they based on past setups that no longer apply?
-
Can you show how worker or supervisor feedback about context was received, documented, and used to update risk assessments, procedures, or controls?
-
Are workers involved in recent reviews, toolbox talks, or fit checks that connect to changes in organisational context? Their involvement is a key audit signal.
-
Are the people using the system able to explain why a control exists and how it relates to their work today — not just in theory or based on outdated assumptions?
The Bigger Picture
Context awareness doesn’t stop at the site gate. What’s happening in one area can affect the rest of the organisation — especially if the system learns from it. Local insight scales up when shared, leading to better decisions, stronger culture, and fewer repeated mistakes.
Every time someone shares what’s changed, the system gets smarter. Every time that input turns into action, the culture gets stronger. And every time leadership listens and responds, trust deepens.
In the end, Clause 4.1 only works if people live it. It’s not just a requirement — it’s a practice. One that keeps the safety system real, relevant, and ready.
Frequently Asked Questions FAQs
Clause 4.1 connects your safety system to the everyday realities of your site. It ensures that changes in people, tasks, tools, or external pressures are recognised and factored into decision-making and controls.
When applied effectively, it reduces the gap between procedure and practice, improves safety relevance, and supports timely responses to new risks.
Context should be reviewed whenever there’s a significant change — such as new roles or staff, tools or materials, client demands, site conditions, or regulatory expectations.
Even minor shifts, like time pressure or weather, can alter risk levels. Regular fit checks and site feedback help ensure these changes are picked up early.
Workers play a key role by sharing what’s changing on the ground. Their insights into daily tasks, risks, and workarounds help shape a system that reflects actual conditions.
Speaking up during toolbox talks or shift briefings ensures that the safety system remains responsive and grounded in reality.
When Clause 4.1 is overlooked, the safety system can become outdated, disconnected, or irrelevant. This leads to mismatches between policy and practice, missed risks, and reduced engagement.
Over time, people stop trusting the system — and that puts both safety and compliance at risk.
Clause 4.1 keeps the safety system alert to change. By regularly reviewing internal and external factors, the organisation can update its planning, controls, and resource use.
This creates a loop of real-time feedback and adjustment — which is the core of meaningful, ongoing improvement in OH&S performance.