The Five Stages of Dysfunction in Workplace Accident Response
From Denial to Accountability: The Safety Culture Response to Workplace Incidents
Workplace accidents are an unavoidable reality across industries, yet they remain among the most dreaded events for safety and operations managers. Beyond the immediate harm to employees, accidents indicate failures in the safety management system, exposing gaps in risk mitigation, compliance, and leadership engagement.
Unlike other operational failures, which are often treated as learning opportunities, accidents result in financial loss, regulatory scrutiny, and legal repercussions. While incident investigation aims to uncover root causes, a dysfunctional safety culture can hinder transparency, leading to missed opportunities for workplace safety improvements.
Although accidents provide valuable lessons for improving safety culture their physical and emotional toll makes them deeply unwelcome. Many organisations focus on accident prevention strategies, yet the effectiveness of these efforts often depends on leadership accountability and a proactive safety reporting system.
How organisations respond to workplace incidents is often dictated by the maturity of their safety culture. A developing safety culture may react with denial, blame-shifting, or superficial compliance measures, whereas a well-established safety leadership framework fosters transparent safety reporting and long-term improvements in organisational safety culture.
Organisations with highly developed safety cultures absorb the emotional shock they bring and respond in line with their highly developed strategies for dealing with accidents and emergencies.
People in organisations with poorly developed or developing safety cultures, on the other hand, respond with choreographed confusion that takes them through denial, anger, bargaining, depression, and finally, acceptance.
This is not an ideal way to respond to accidents and emergencies.
Stage I: Denial – The Initial Reflex to Hide the Truth
The very first stage of response to accidents is both denial and, sometimes, immediate attempts to cover it up. This is the '...since no one else saw it, let's keep it between us' type approach.
This attitude is pervasive in developing cultures and is only shed when cultures reach a level of maturity where they are confident in their own processes and capable of owning their mistakes.
This cultural blemish is also a product of the business and, sadly, regulatory environment that many operations exist in. As more organisations claim to be adopting a blame-free safety approach to their operations, our regulatory frameworks remain firmly blame-friendly. They compensate the victim and punish those deemed to have caused the accident where negligence and other factors are suspected.
The fear of operating in such environments is made even more palpable with the high potential for personal jeopardy for company officials, in addition to the impact on the operations as a whole.
The direct impact of this oxymoronic situation, where the very elements required for sustaining a learning organisation are also the ones that pose the most significant personal legal risk to operational team members, is that many choose to be safe rather than sorry, and to hide rather than admit.
In further-developed safety cultures, there is a level of confidence in the robustness of their processes and, therefore, an ability to stand up to scrutiny. Such operations teams avoid this denial and are upfront about their performance statistics.
This denial phase only lapses once a realisation hits that the news is already out. Pictures have hit social media, and burying the head is no longer a viable strategy.
Stage II: Anger – The Blame Game Begins
With the denial over and often in its afterglow, anger erupts. Fingers are pointed in all directions—at the victim for falling victim and not taking extra care.
At the supervisor for not being everywhere at the same time. At the storekeeper who should somehow have known not to issue the tool to the victim. At the safety manager for not intervening on time. And pretty much everyone else. The feelings are usually mutual, as every person blamed has a retort and a spin that absolves them.
This multi-directional anger that cancels itself out is again a product of the operating environment, where accidents are so unwanted yet so common. Each accident shatters the last target of zero accidents, only for the clock and targets to be reset until the next accident.
Anger at the victim or anyone else is conspicuously absent in further-developed safety cultures. They see accidents as a failure and, at the same time, an opportunity to learn and grow. Confidence in their application of effective management processes dispels the fear that triggers anger in other teams.
Stage III: Bargaining – Crafting the Narrative
As the embers of anger cool and the reality of what follows hits, team members in developing safety cultures come to a reckoning on the need to proceed with the next stages. With the victim off to the care of medical practitioners and the onlookers dispersed, it is time for the spin doctors to weave a compelling story.
A story whose goal is not necessarily the truth but a version of events that the spinners want to tell. Facts may be added or removed from the story to fit the preferred narrative. Without even venturing near criminality or flagrant ethical destitution, verbal and written narratives of the accident can be contorted to present an elevation that paints the picture the team feels comfortable with.
This creative storytelling is exactly why most accident investigations rarely result in uncovering the true nature of accidents and learning opportunities from them.
This desire to tell a preferred story instead of the real story is not a slight that should be despised too easily. This is a direct consequence of the environments teams operate in.
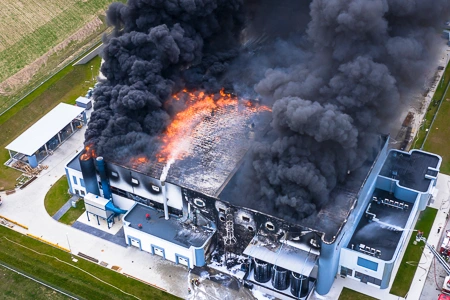
To err is human. Yet we place humans in highly complex operational environments and then engender zero-accident targets that are never paired with limitless budgets. When their innate propensity to err strikes, managers and regulators are waiting to point fingers. Yet we expect open and totally honest reporting. Good luck!
What we get is as honest a level of reporting as the environment can produce. In further-developed safety cultures, accidents and targets around them are tethered to the reality of the operating environment. Their success is not dictated solely by accident frequency rates but by a holistic analysis of their performance.
Developing safety cultures do not have the luxury of holistic analysis. Partly because there is nothing holistic about their approach to start with. These teams run on luck, and when their luck runs out, they panic because any thorough accident investigation will uncover a system of failures associated with the accident. So telling a preferred story is an adaptation for such operations teams.
Stage IV: Depression – The Weight of Uncertainty
A major downside of telling preferred stories and running on luck is that the risk of being found out is never far away. These teams are great sufferers of the aptly named imposter syndrome—scratch beneath the surface, and all is exposed.
The depression comes from the fear of being found out. It also comes from the loss of the facade they have maintained so far—excellent safety scores, awards, and apparently engaging safety programmes. And it must also come from the knowledge that they have let the victim down, as their collective failure led to the accident.
These depressive states are not common in further-developed safety cultures, where accidents are seen for what they are—a failure that doubles as a learning opportunity. They are confident in their systems, already aware of what failed, and happy to share full details with regulators.
Stage V: Acceptance – Moving Forward or Stagnation?
Depression eventually gives way to acceptance. The run of accident-free man-hours has been broken, again. The doctor's recommended rest cannot be ignored by bringing the worker back in some restricted work manner. Team members move on as the chapter is largely closed. The internal accident investigation process is for the records; everyone knows what happened.
As the team returns to baseline, they tend to return to the same practices that led to the accident. This often happens because those practices are structural and dictated by the operating environment, which encompasses the prevailing safety culture.
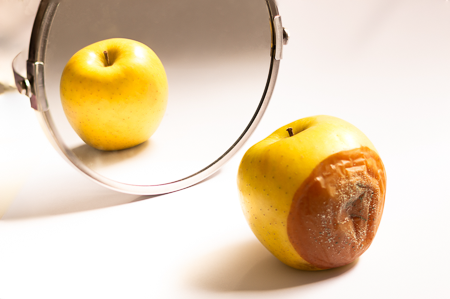
In further-developed safety cultures, acceptance comes in the immediate aftermath of an accident and concerns focus early on the victim and the failures that led to the accident. Where personal lapses are identified, robust conversations are had, and attention moves to improvements to prevent reoccurrences.
Where systemic issues are identified, systemic solutions are devised and rolled out. Fulfilling specific regulatory requirements is swift and left to those designated to handle them, whilst the team returns to safe production, confident in their knowledge that the accident was an aberration unlikely to be repeated. This is an approach that developing cultures cannot yet match.
Breaking the Dysfunctional Cycle: Creating a Learning Safety Culture
Whilst the foregoing may appear to paint an overtly negative view of developing cultures, it is important to note that these cultures are not necessarily reflective of the character of the people in them. They are instead reflective of the often-ignored impacts of the prevailing environment on operations teams.
When a team is under-resourced yet expected to deliver at scale, the imbalance produces pressures that must be released somewhere—either to the detriment of the health of team members if they allow it, or to the detriment of operational goals, including safety targets. This is a reality of the way things work. Imbalances create inconsistencies.
Furthermore, many further-developed safety cultures have, at some points in their history, gone through bygone eras they are not proud of. All safety cultures exist on a continuum, where cultures further along the line have shed the negative elements that cultures behind them are yet to shed. The more open and inclusive a safety culture becomes, the more confident it gets, and that bodes well for its operations.
In all, dysfunctional responses to accidents are a negative burden on operational teams. They are juvenile and ebb with time and effort. The key duty of the practitioner, as a mentor to operational teams, is to identify where their team is on the safety culture continuum. Then, acknowledge the inescapable realities of that state and advise on the enormity of resources—time, money, mindset changes—that are needed to move forward.
Cultures do not exist in isolation. They exist in the operating environment that we are all explicit or implicit contributors to. Every effort expended in elevating safety management practices, for example, contributes to a better operating environment for all teams. Likewise, every effort spared in making regulations smarter and more adept at adapting to the changing nature of work is a net loss that degrades the operating environment for teams.
We are creatures that err, operating in complex environments with competing interests, with the goal of creating a better world. All the flaws highlighted above are as human as the ideas of what better looks like. It is all us.
At SafetyRatios, we connect incident response with cultural safety metrics to enhance workplace accident management. This article explores how safety cultures react to workplace accidents, from denial to accountability, and the challenges that arise in each stage. For solutions that strengthen incident tracking and real-time safety insights, visit our Solutions Page and explore our analytics-driven safety tools.