Zero Accidents: Is It a Mindset or a Metric?
Decoding the Safety Industry’s Biggest Debate on Achieving Zero Accidents
Target zero, goal zero, towards zero, beyond zero—zero is the most common target in nearly every major corporate safety programme today. Each organisation makes its case for it; some invest heavily in it, while many boast of its accomplishments and successes.
Proponents highlight the transformative power of these programmes in bringing safety to the forefront of organisational priorities. Critics, however, remain sceptical—often questioning the feasibility of such a goal, citing real cases of accidents occurring after long periods of zero incidents within corporations following the programme. Fence-sitters are ambivalent; to them, zero-accident programmes work—until they don’t.
A common theme across many of these initiatives is the conflation of mindset zero and metric zero. The mindset zero partly emerged as a response to critiques about the attainability of metric zero. After all, striving for zero accidents year after year while reporting incidents inevitably raises questions. The common defence? Zero accidents is a mindset, a vision, an approach, a commitment, a pledge—everything but a number.
Reading through many corporate programmes today, it remains challenging to determine whether a company is aiming for mindset zero, metric zero, or perhaps both.
So, when is zero not really zero? While that may sound like the start of a bad safety joke, the fundamental question remains: Is zero accident or zero harm truly attainable?
Zero Accidents: A Possible Reality or an Unrealistic Goal?
Sustaining large-scale operations for extended periods without accidents is possible. A highly skilled and well-motivated workforce can accumulate millions of work hours without a single incident.
There are documented cases of such achievements, and dismissing them outright would unfairly discredit those who have accomplished them. The concept itself is not inconceivable—stack enough safe hours together, and over time, they can add up to millions without an accident.
Rare, difficult, and highly demanding—but not impossible.
Zero Accidents: Why It’s Rare Despite Industry Efforts
While achieving zero metric accidents is possible, it remains exceedingly rare in the industry. This is supported by publicly available workplace fatality statistics, which show a plateau—and in some regions, an increase—in workplace fatalities and major accident rates over the past decade.
These statistics focus on fatalities and major accidents, which make up only a small fraction of all workplace incidents, the majority being minor. Notably, this stagnation in accident trends coincides with the widespread adoption of zero accident programmes.
Understanding why zero metric accidents are so rare requires an appreciation of the complex and unpredictable nature of workplace accidents, which are often more intricate than they appear.
Modern workplaces are dynamic environments where time and cost pressures collide with competing interests, differing work styles, and shifting priorities.
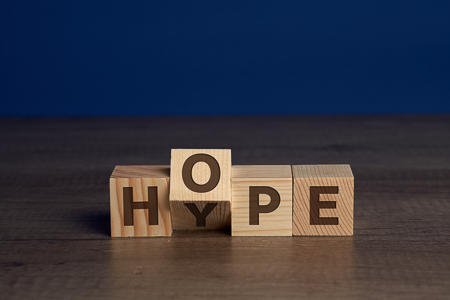
No two days are ever the same—especially in industries like construction, where zero accident initiatives are common. Delays are routine: materials arrive late, storage areas aren’t ready, the crane has been reassigned, inspectors refuse to sign off, site manager wants his crew back, and the safety officer has just found another issue with the proposed delivery route.
These are all factors that contributed to accidents, yet site teams navigate these challenges daily—often without an accident.
However, maintaining this level of control across countless operations, avoiding every accident without eliminating the very factors that contribute to accidents, is an extraordinarily difficult task.
Is It Luck or a Strong Safety Culture? The Field Perspective
From safety solution vendors to consultants, executives, and even safety practitioners, everyone prefers the narrative that their safety programme has significantly reduced accident levels. Their collective favourite tool? A "strong safety culture." Although safety culture is an emergent construct that develops over time, some teams seem to have mastered the art of willing it into existence almost instantly.
The reality, however, is that luck plays an integral role in many safety management systems—yet it is rarely acknowledged. Every team needs a bit of luck, and that is not inherently a bad thing. The problem arises when luck becomes the unspoken foundation of a safety record. Accidents are complex; the same set of conditions does not always lead to an incident, unlike the predictable equations of physics.
For example, materials might repeatedly fall from an unprotected edge onto a busy lower ground without causing an accident. That is luck in action. Yet too often, this randomness is masked by an industry mindset that prioritises counting accidents over identifying and addressing the factors that contribute to them.
A workplace where accident-inducing factors are neither recorded nor controlled may report long stretches of safe man-hours—but that success is down to luck, not a strong safety culture. In truly developed safety cultures, the focus shifts from counting accidents to addressing the underlying factors that cause them. As a result, the targets extend beyond both mindset zero and metric zero.
Mindset Zero: Can Thinking Safe Actually Prevent Accidents?
Critics of mindset zero accident programmes argue that achieving mindset zero target is an easy task—at least on paper. Their core argument is that the programmes' primary deliverable appears to be a commitment to achieving zero accidents—a goal as simple as declaring a desire to become a millionaire by 30.
Their main evidence? Very few organisations running these programmes allocate the time and resources necessary to truly uphold such a commitment. To genuinely prevent all accidents, an organisation would need to dedicate matching (unlimited) resources to safety—something that is inconsistent with industry realities, where competing interests and economic constraints limit the time and funding available for safety initiatives.
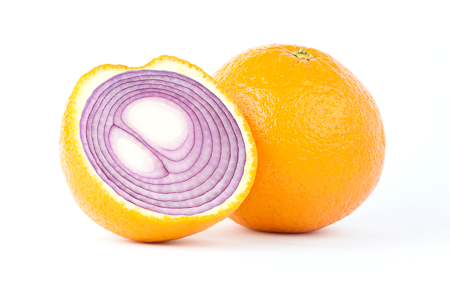
Proponents, however, argue that the mindset shift itself is the goal. Establishing a positive safety culture across an organisation is a victory, and the benefits of such a shift ripple outward—shaping how employees, investors, customers, and other stakeholders perceive the brand’s commitment to workplace safety. They also point to the ethical necessity of committing to a zero accident mindset as the direct opposite of accepting that accidents and injuries are an unavoidable cost of doing business.
From a field perspective, mindset zero accident programmes do improve safety performance in the short term. However, confusion around chasing a goal that is sometimes unclear—or perhaps unattainable—can erode their long-term effectiveness.
Metric Zero: Is Total Accident Prevention Achievable?
Metric zero is a far more complex target, even though it appears simple—an operation with no accidents. Critics argue that complexity arises when the definition shifts from "zero accidents" to "zero serious accidents" or when it becomes an ongoing goal, regardless of whether it is met. They emphasise the importance of setting clear and attainable objectives, a well-established principle in goal-setting.
Some go further, claiming that zero accidents is fundamentally unattainable due to the complexities of the workplace and the infinite variability of worker motivation, mood, beliefs, and the behaviours they drive. A common argument is: What can anyone do about a carpenter who aims at his own finger?
Proponents of the metric zero accident target take different positions. Some present it as a tangible goal, arguing that all factors contributing to accidents can, in fact, be controlled—making all accidents preventable and, by extension, making metric zero attainable.
Others focus instead on the value of the target itself, regardless of whether it is met. They conclude that setting a metric zero accident target is inherently valuable and ethical, with the act of striving towards it being more important than the actual outcome.
From a field perspective, metric zero is attainable but requires a level of resources beyond what most organisations can commit. It also demands significant changes and evolution in various aspects of the workplace. A highly developed safety culture can achieve metric zero accidents, but such a culture does not exist in isolation. As other cultural forces within the organisation and its environment shift, so too does the safety culture—sometimes making metric zero accidents unattainable.
In conclusion, neither dismissing zero accident programmes as hollow gestures nor fully embracing their metaphorical targets at the expense of empirical accident data will enhance an organisation’s safety performance. A holistic approach that combines the motivational power of mindset zero with the structured, measurable objectives of metric zero offers a more balanced and effective strategy.
Achieving both mindset zero and metric zero is possible, but sustaining them requires a genuine commitment of time, resources, and continuous effort.
At SafetyRatios, we challenge conventional safety norms and redefine safety metrics by bringing real-world site insights into thought leadership. This article is part of our rethinking approach—for our metrics-driven solutions, explore our Solutions Page and take advantage of our free trial programme.